Andel Plastics and BioTAK have seen the launch of the new WASHtAK product after over six years research design and investment in the product.
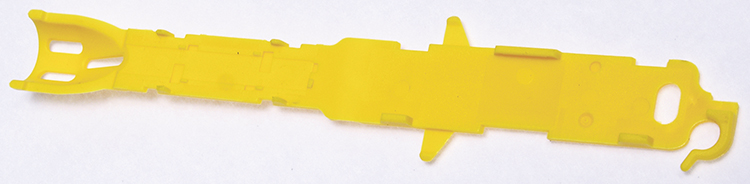
part
WASHtAK is a new product designed to manage, monitor, and optimise clinical wash processes, driving up standards in hospitals around the world.
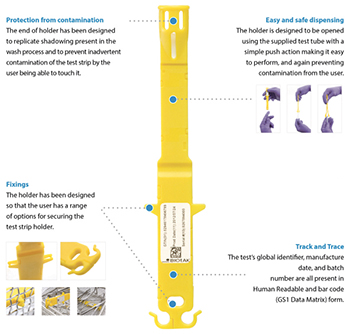
Currently, after a clinical wash the operators check for residues of blood, etc, on the instruments but there is no real quantifiable way of ensuring the instruments are indeed ‘clean’ until now. The plastic injection moulded WASHtAK, with its unique TAK enzyme strip, sits within a wash chamber, for example of surgical instruments after surgery. This is then analysed after use to assess whether the wash was indeed successfully ‘clean’ – a new innovation in the world of healthcare and the way forward for the future.
The project started with an enzyme coated strip, the enzyme would be within the clinical wash of instruments. The core idea behind this is that you have a known starting load of enzyme on the test strip, the better the wash the less enzyme will be present afterwards. Contamination from handling the test strip can alter results, so it was clear that in order to make this a viable product within the wash situation it would need an appropriate holder.
Plastic, being relatively cheap and effective, was chosen for the style of holder and Graham Robinson, then of Malvern Healthcare, was contacted with a rough sketch of an idea for a hinged component that would house the strip safely in the wash and dispense it appropriately when required.
In order to keep the product simple and cost-effective, Graham helped come up with a different component design that would make tooling more economical and provide all the holding and clipping features of the product for each environment that it was being designed for. This design for manufacture process eliminated over complicating the tooling and component and produced a cost effective design for both.
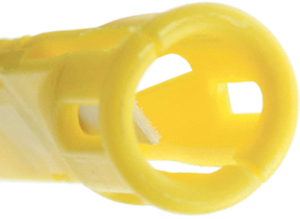
The end result was to make two halves of a moulding, with integral clipping features and a place for the enzyme coated strip to sit safely, whilst still sitting freely in the wash, but without risk of contamination by being touched.
After a prototype tool was manufactured the product was tested by the Health Protection Agency by assembling small batch runs. Thus proving what alterations needed to be made to ensure a quality reliable product. Production was then moved to Andel Plastics Ltd when Graham became Technical Director there in October 2012. “I was really pleased that BIOtAK followed me in my new venture, as the product has always excited me and it’s so good to see a product go from concept, through all the testing and tweaking, into full production. It’s a really simple clever device that will solve a complex issue.”
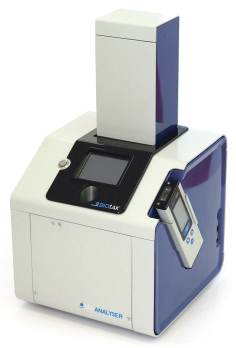
Since then things have continued to develop with a production tool being manufactured at Andel Plastics in house toolroom. The first major production run of this product has just been completed ready for launched trials with the NHS and European Hospitals.
For the assembly of the enzyme strip into the new WASHtAK holder a Class 8 Clean room was required, with the aid of the Business Innovation Programme, Andel Plastics was able to secure match funding for this investment. The installation of the cleanroom took a very swift three months from start to full certification and is now catering for two Medial Device customers.
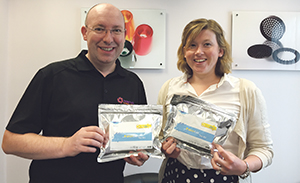
Why then is this product so exciting and why has it has taken over 6 years to bring to market? The component design and manufacture is an everyday occurrence for Andel Plastics and its core business. So how do you assess the enzyme on the strip? Rather than relying on objective comparison to a bottle label, as many such strip tests do, BioTAK wanted to launch a state-of-the-art fully traceable system, with quantifiable results and immediate results. After considerable investment, research and development, there was borne the TAK analyser with a barcode scanner for full traceability and a USB output for storing data. Using the easy dispensing method designed into the WASHtAK holder, the uncontaminated strip can be taken straight from the wash, scanned, assessed and give a reading within minutes. Knowing instantly whether the wash is successful and the instruments are indeed safe to use patients. Joanne Harmer of BIOtAK said, “The whole aim was to give accurate, quantifiable results, straight after the wash, driving up standards and driving down costs for the NHS and other healthcare operators.”
Andel Plastics also manufactures the addition to the range of an Endoscope holder called the LUMENtAK, but a larger range of TAKs for chamber decontamination is planned now the technology is proven and the quality assurance of the brand is there. Again being designed and developed in the UK by Biotak with manufacture being completed by Andel Plastics at its newly expanded Birmingham premises.
T +44 (0)121 765 4042
F +44 (0)121 706 3917
www.andelplastics.co.uk